The role of DFMA in product design
DFMA is a harmonious combination of Design for Manufacturing (DFM) and Design for Assembly (DFA). DFM focuses on the ease of manufacturing a product, while DFA aims to simplify and shorten the assembly process.
Both methodologies have similar objectives, but there may be situations where one conflicts with the other. For example, optimizing the DFM can compromise the efficiency of the DFA, and vice versa. To avoid such conflicts, the DFMA uses both the DFM and the DFA in a complementary way to achieve an optimal product design.
The main aim of DFMA is to reduce the time, cost and effort required to produce a product. By optimizing factors such as materials, manufacturing processes, volume, machines, tools, precision, number and complexity of parts, manpower and skills, automation potential, etc., companies can reduce initial costs by over 50%.
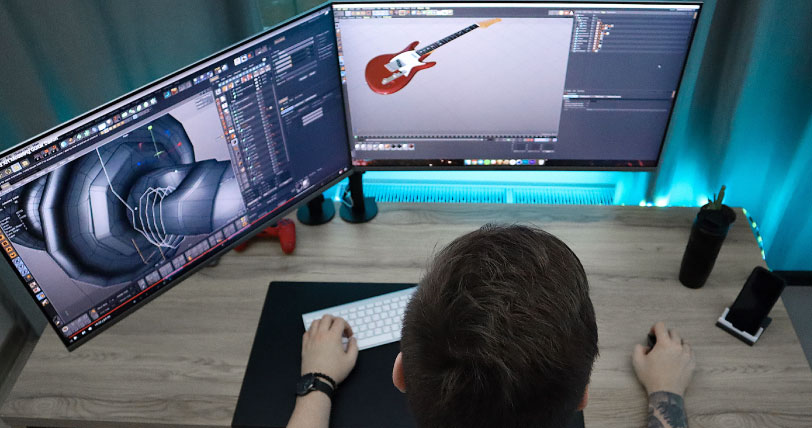
The advantages of DFMA
The application of DFMA offers numerous short- and long-term benefits. These advantages are essential to creating a strong, competitive product on the market. Here are just a few of the remarkable advantages of DFMA:
Shorter time-to-market
Time-to-market is the period between idea generation and product introduction. DFMA significantly reduces this time by simplifying manufacturing processes and assembly steps.
Reduced product development costs
Effective application of DFMA from the outset reduces development costs by anticipating and resolving potential problems that may arise at a later stage. By avoiding downstream design changes, DFMA also saves time and resources.
Reducing waste
DFMA aims to eliminate waste in product design and assembly. It reduces material waste, unnecessary movements, excessive inventories and redundant manufacturing and assembly steps. It also minimizes the risk of defects and waiting times.
Improved product reliability
Thanks to increased attention to defect prevention and cost-benefit optimization, products designed according to DFMA principles are naturally more reliable and durable. The reduced number of parts in a DFMA product also contributes to a lower failure rate.
Quality control
DFMA improves communication and collaboration between the different teams involved in a manufacturing process. Efficient coordination between designers and manufacturing engineers enables a higher level of quality to be achieved within budget.
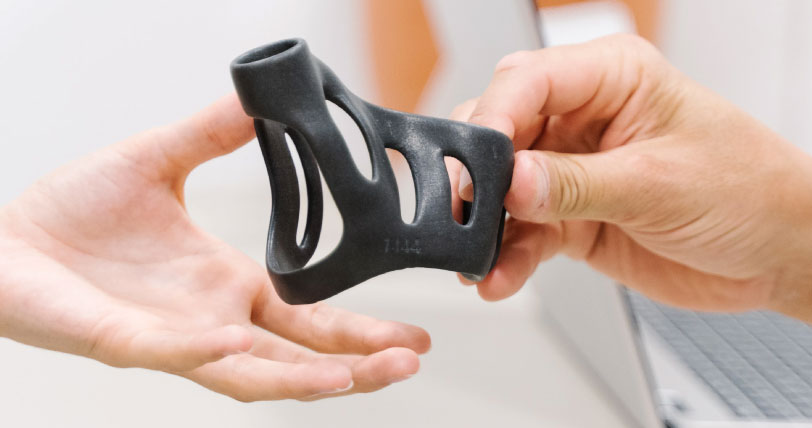
The principles of DFMA
The DFMA is based on several principles that guide the application of this methodology. Here are some of the principles commonly used in the DFMA:
Simple design
Simplicity of design is one of the key principles of DFMA. A designer should strive to create a clear, efficient design by eliminating superfluous features and components. A simple design is generally easier to manufacture and assemble, resulting in lower investment costs and relatively shorter manufacturing and repair times.
Modular design
Modular design involves dividing a product into different modules, each fulfilling a specific function. This approach reduces the number of parts needed for a product family. For example, a single laptop battery can be used in several laptop models. This approach reduces costs, time-to-market and inventory, and facilitates future customization and upgrades.
Easy, efficient fastening
Most products require the use of a variety of fasteners. DFMA optimizes this process by recommending fasteners that are affordable, easy and quick to install. Wherever possible, it favors the use of interlocking fasteners. Rivets can be preferred to screws for a stronger connection. Careful attention to fastening methods can reduce manufacturing costs, waste, product weight and space requirements.
Poka-Yoke
Poka-Yoke refers to the use of error-proofing techniques to improve the precision of manufacturing and assembly operations. The aim is to correct errors and defects as soon as possible by installing automatic or manual devices that prevent incorrect assembly of product parts. These devices ensure that each component can only be assembled in the correct orientation. The use of asymmetry in the product structure is one of the methods used to achieve this objective. However, it is important to note that symmetrical products are easier to manufacture and assemble.
Reducing the number of parts
Reducing the number of parts is one of the most popular DFMA techniques. This has many advantages, including reduced manufacturing and assembly time, and reduced risk of incorrect assembly.
Use of standardized parts
Standardized parts are easier to find, cheaper and more reliable than custom parts. The DFMA recommends the use of standardized components wherever possible.
Knowledge of process limits
It is essential that designers are aware of the different manufacturing processes and their capabilities when designing a product. DFMA improves communication between the different teams, to ensure that decisions taken take into account the most economical manufacturing methods.
Customized tolerances
Strict tolerances can be difficult to achieve, requiring costly production and measuring methods. In addition, parts with tighter tolerances are more difficult to assemble, resulting in higher labor costs and scrap rates. Wherever possible, tolerances should be as wide as possible to reduce costs while maintaining functionality.
Other DFMA techniques
In addition to the principles mentioned above, there are other DFMA techniques that improve ease of manufacture and assembly, such as the elimination of flexible parts, automation of the production process, modifications to facilitate assembly, consideration of part handling and orientation during manufacturing and assembly operations, and the design of multifunctional parts.
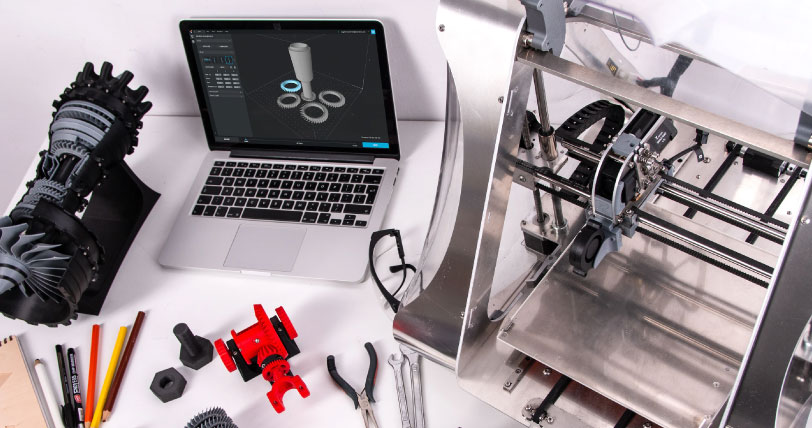
Conclusion
Design for Manufacturing and Assembly (DFMA) is an engineering methodology for optimizing the manufacturing and assembly aspects of a product. By combining the principles of Design for Manufacturing (DFM) and Design for Assembly (DFA), DFMA aims to reduce costs, improve quality and accelerate the time-to-market. By applying DFMA principles, 1POINT61 can design products that are simpler, more reliable and more economical to produce.